4 min read
MIPI in IoT: Enabling the Enterprise Drone Market
Ian Smith, MIPI Alliance Technical Content Consultant
:
11 May 2021
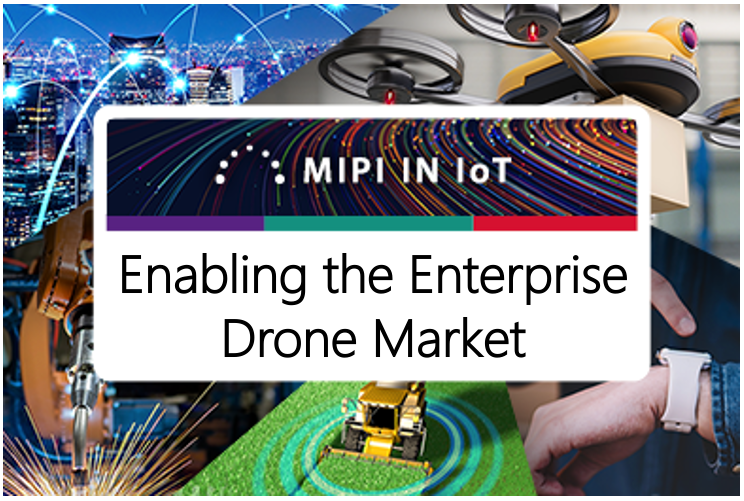
- News & Events
- News
- Blog
The scope of the Internet of Things (IoT) is vast, covering numerous consumer and enterprise market sectors. For a closer look at how MIPI Alliance specifications support growth in IoT, we're taking a look at a different IoT market sector each month. In this third post in the series, we’ll examine the use of MIPI specifications in the enterprise drone market.
Overview of enterprise drones market
In 2021, the European Union Aviation Safety Agency and US Federal Aviation Administration issued new regulations, clarifying the legal landscape for drone usage and setting the goal of integrating drones into existing airspace while maintaining the necessary safety levels. With the release of these rules and similar rules in other countries, the global enterprise drone market is expected to grow at a significant rate over the next decade.
Analyst reports indicate that the use of drones in the enterprise market will generate most of the value in the broader drone market—enterprise drones being defined as “unmanned aerial vehicles (UAV) sold directly to a business for use in its operations.” Based on this definition, analysts predict the total global shipment of enterprise drones will reach 2.4 million units in 2023—a 66.8% compound annual growth rate (CAGR)—with the main source of growth occurring in five main enterprise market segments:
- Agriculture
- Construction and mining
- Insurance
- Media and telecommunications
- Law enforcement
Machine vision: a key technology enabler for high-value use cases
The use of high-resolution machine vision is essential for many enterprise use cases, such as using drones to perform the remote inspection of power lines and telecommunications towers, monitor crops and livestock, perform industrial site inspections and enable law enforcement reconnaissance.
Machine vision also provides a much more fundamental enabler to unlock the highest value use cases in the enterprise drone market: the ability to operate drones beyond the visual line of sight (BVLOS)—i.e., for drones to navigate themselves autonomously, well beyond the visual range of the drone operator, connected via wide-area cellular and satellite.
Drone experts have highlighted the development of detect, sense and avoid (DSA) systems as being critical technology enablers for BVLOS drone operation to ensure the drones can maintain compliance with regulations. These systems reduce the risk of a mid-air collision by ensuring the drones are able to operate safely in a variety of environments and avoid obstacles, including other aircraft.
A key component of these solutions will be the integration of high-resolution cameras, lidar and radars. The data from these sensors will be fused, using cellular connectivity, with data from other UAVs or ground-based systems so that the drone has a good understanding of its environment and is able to safely maneuver within it.
The key challenges when developing drones with advanced machine vision and DSA capabilities are designing and integrating sensors and their associated compute components within necessary performance, size, weight and power constraints. Use of MIPI specifications within these components can help overcome these challenges.
MIPI specifications: solving technology challenges
MIPI Alliance develops and maintains interface and protocol specifications to connect key embedded electronic components (cameras, displays, sensors and communications modules) within electronic devices. The specifications support design goals of high-bandwidth performance, low power consumption and low EMI. Described in more detail below, the following attributes allow MIPI specifications to enable enterprise drones that require machine vision and solve key technology challenges involved with the implementation of DSA solutions:
- High bandwidth: MIPI specifications define high-speed, highly scalable, ultra-low-latency interfaces for connecting electronic systems and components. The interfaces provide highly data-efficient modes of operation to support the requirements of a wide range of imaging and sensing components, from the most advanced cameras to the most basic, low-speed sensor components.
- Low power consumption: MIPI specifications enable highly power-efficient and flexible data transmission between components. The specifications enable very low power consumption in “active” modes when data is being sent and received, in ‘’active-standby” modes when data transmission is low and interrupt-driven, and in "full-standby” modes when there is no data transmission.
- Low EMI: Drones need to meet strict EMI design goals, both to ensure product reliability and to adhere to strict, sector-specific electromagnetic compatibility (EMC) regulations. MIPI specifications reduce EMI through a combination of factors, including low-voltage swings on high-speed physical layers and the support of slew rate control—giving developers the flexibility to adjust the EMI profile of the physical layer interface to the EMI needs of the end device. These EMI properties also reduce product weight, requiring less EMI shielding.
- Low size and weight: MIPI specifies high-performance serial interfaces that use a minimum number of wire conductors to allow designers to minimize pin counts—leading to fewer interconnections on chips and across printed circuit boards. The resulting reduced complexity supports the ever-tighter packaging of components and, critically for drones, reduces the weight of the overall design.
- 5G ready: MIPI specifications are future-focused to meet the demands of forthcoming requirements. MIPI specifications are already capable of supporting 5G services, including Enhanced Mobile Broadband, mMTC and URLLC.
- Security: MIPI recognizes that security is critical to the drone market, where devices must adhere to strict functional safety standards. The MIPI Security Working Group is overseeing the development of a MIPI security framework that will steer the development of new security capabilities across MIPI’s specification portfolio.
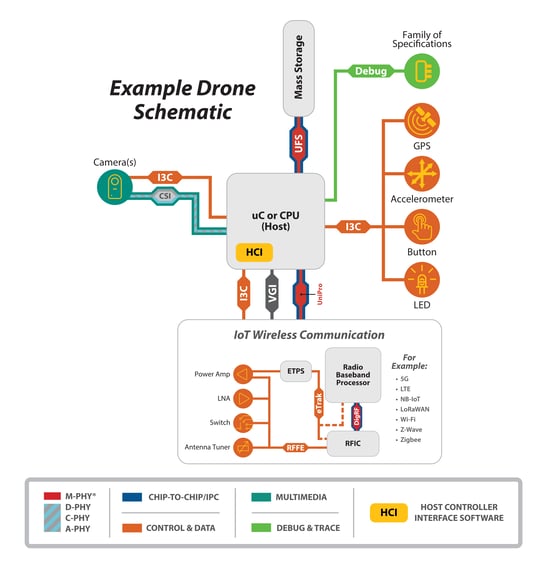
The following MIPI interface and protocol specifications are most relevant to the enterprise drone market:
- MIPI CSI-2® provides a highly scalable protocol for connecting advanced high-resolution cameras, lidars and radars, enabling low-power vision inferencing and machine vision.
- MIPI C-PHY℠ and MIPI D-PHY℠ are low pin count serial interfaces that can be used to connect high-speed sensors in smaller drones where line lengths are <50cm.
- MIPI A-PHY℠ provides an ultra-reliable, long-reach (≤15m), serial interface that uses coax or STP cables to connect high-speed sensors in large drones.
- MIPI UniPro® enables Universal Flash Storage (UFS) that can be used to store high-resolution video locally on a drone.
- MIPI I3C® provides a shared, two-wire, low-weight, medium-speed serial interface to connect the sensors, actuators and controls required to operate a drone. MIPI I3C can be implemented over MIPI A-PHY as an ultra-reliable, long-reach, physical interface in noisy EMI environments with minimal EMC shielding.
- MIPI RFFE℠ is used to control RF front-end components within wireless communication modules, including power amplifiers, low-noise amplifiers, filters, switches and antenna tuners.
Learn more
For more information on how MIPI specifications are enabling enterprise drones and to see examples of other IoT use cases, download the recently published white paper; “MIPI Alliance: Enabling the IoT Opportunity.”
You can also access the MIPI DevCon 2020 IoT presentation and closing chat session to hear from industry experts about the growth of IoT, market trends and the role of MIPI specifications in supporting connected devices.